近年來,隨著精實生產概念的引入,大部分製造業開始爭相學習這種生產模式。在起初一到兩年的實踐過程中,在成本層面會有部分減少,但是在第三年左右開始,雖然依舊存在改善的點,但其成果無法在財務層面直觀呈現,精實生產模式的匯入也不得不在此中止。很多時候我們不得不質疑,這種生產模式是否真的契合自己的企業,或者說這種概念只是徒有其表。
一、淺析精實生產模式及其實踐現狀
1、何為精實生產模式
精實生產前身為豐田模式,這種模式是當時豐田為應對美國大批次生產模式、基於自身國情及市場而探索出的成果,其最初的核心主旨為:不用擔心錢的問題,縮短過程時間是豐田的原則。漸漸迭代為如今由準時化及自動化兩大支柱構成的精實生產模式,而踐行精實生產模式的企業即為精實企業,如下圖所示:
2、製造業現狀解析
無論對於製造業還是絕大多數的企業來說,核心的目標均為:降本、提質、增效。而三者的權重及實踐路徑並沒有被完整定義,相互之間也並沒有進行資料的串通,大部分企業的經營發展及內部績效的評定依舊由純財務資料支撐。雖然財務資料的衡量具有絕對的標準型及成果可視性,所達成的結果我們稱之為:區域性最優,但其弊端也會逐漸顯露。
何為區域性最優?在這裡我們舉一個簡單的例子:當“降本”作為企業的經營重心時,分發給各業務部門的指標也不盡相同。對於採購部而言,以更低的價格採購物料便為其目標,而在同供應商談判的過程中,提高採購量即是最有效的降價途徑;對於生產部門來講,減少換線次數,採用大批次生產的模式,其生產成本也會大幅下降;再比如對於銷售部門而言,實施大批次銷售,降低銷售費用也是最具有可行性的降本措施。
以上種種行為的結果自然是每個部門的財報中都會體現相應改善行為在降本層面做出的卓越貢獻,而大批次的雛形也在此時開始浮現,庫存的增加,產品的週轉減慢,而各個現場依然會繼續進行“降低進價”、“簡化生產工序”、“尋找便宜的倉庫”,持續推進完全獨立的、區域性最優的降本活動。最終,各部門的成本降低了,但從公司整體來看,原材料倉、半成品倉、成品倉的增大,物流週期的拉長,大訂單的不穩定性增加,種種情境會導致企業內部出現巨大的損失。
3、精實生產的推進困境
正如我們在文初所提到的,精實生產的理念在初步引入企業內部時,確實會在成本層面有部分成果。但當我們僅侷限於成本層面,由此點出發去套用精實理念時,其結果也同改善前的狀態如出一轍。
其實精實生產的改善方式其出發點絕非成本,而是透過自動化在確保質量的基礎上,徹底實現縮短過程時間,進而帶來收益。
所謂過程時間,在財務層面又如何去量化,才能體現出企業在實踐精實生產過程中的變革,得到高層的認可以繼續推行該種生產模式。這時候我們就需要引入新的指標,新的“X軸”——時間。
二、“時間“之於”賺錢能力“——收益性
1、庫存的收益性損失
低庫存始終為貫穿精實生產理論的生命線之一,製造型企業也在大力推動降低庫存的措施,而後者往往會直接透過現金流的穩定性及庫存轉化為資金後的利息損失,來衡量庫存健康程度,其關注的指標通常為庫存週轉率及呆料在倉天數,而長期持有庫存會給客戶帶來什麼樣更深層次的風險,即“一萬元的庫存停留一天,會帶來什麼樣的損失”,我們始終缺乏一個明確且細粒度的指標來衡量。
在這裡我們引入一個小場景來細化一下何為收益性。
假設有四輛庫存單價為44W的小轎車準備發往某處經銷商,一輛單趟運輸成本為2w的貨運車容量為5輛小轎車,而還有一輛小轎車將於第二天生產完畢。這個時候我們都會選擇第二天將五輛汽車同時運走,因為此時會降本20000/4-20000/5=1000。
而精實生產的前身——豐田生產則是無條件縮短過程時間,即第一天將四輛汽車運走。可能在傳統會計思維下我們無法理解這種行為,這裡我們引入新的指標:庫存毛利率=每年產生毛利/庫存/365,即假設公司不會讓庫存停留,每一天都在賺錢,此時一萬元的庫存每天會帶來多少的收益,反之庫存多積壓一天便會少賺相應的錢。
利用這個公式我們回到前面的問題,豐田08年的年庫存毛利率為806%,也就是每1w的庫存,工作一年可以賺到80627元,即一天可以賺到221元,而如果多保有一天庫存,就會有221元的損失,那麼此時我們讓題目內的車多停放一天,相當於損失9724元。此時我們將1000元同9724元相比,便可以看出兩種方式下豐田為什麼會選擇無條件縮短過程時間。不過需要指出的是,在庫存層面,收益性指標的價值在於放大庫存的積壓問題及實行相應改善後的結果反饋。
2、速度同金錢的衡量法則——收益性惡化率
在運輸層面,傳統模式我們都會選擇為降低成本而選擇運輸費最低的物流方式,但是,那些高昂的、快速的運輸方法必然有其存在的意義。結合精實生產我們知道加快物流速度,庫存就會減少,這也是我們需要改善的點,但是結合實際情況,企業具體應該在運費上多支出一些,以實現快速運輸,還是多花一些時間減少運費支出,此時相關人員很難做出正確的判斷,這個時候我們將物流後出售收益性及公司門口(不存在物流)收益性惡化率對比,,進而判斷收益性惡化最低的方案。
收益性惡化率=(1-運費比)/(1+過程時間比);
其中,運費比=運費/毛利;
過程時間比=運輸過程時間/製造過程時間;
可以看出,商品的毛利越高,運費對收益性惡化率的影響越小。再比如像糧食這種需要至少半年才能收穫的產品,運輸時間達到30天也不會有過大的影響,而製造業目前基本在兩個月內就可以完成生產,這意味著分母變成了1.33,而我們推進改善,減小庫存,便可以與物流相同的20天完成生產,這樣分母就變成了2.0,收益性惡化率降到了一半以下。
同樣,我們可以利用此公式計算比較外企選擇在中國生產以及本土生產的收益性惡化率,在算上運費及運輸過程後,反而有些情況在中國使用較為實惠的勞務費卻不如在本土生產。
3、企業整體收益能力評價
之前兩個指標我們是對現場改善結果進行評價,那麼如果從全域性即企業整體評價出發,如果經由財務分析,對準時化進行評價,才能真正體現企業的實踐成果。
這裡我們首先引入資本利潤率的指標,財務層面我們常常以這個指標出發衡量企業收益率,但是它所設計的指標:利潤總額、本期淨利潤、總資本指標等,無法直接反應生產現場的實力,而更大部分的受該企業財務效率以及債券回收能力的影響。
在這裡我們需要將其公式進行進一步的改造:
收益性評價指標 = 銷售總利潤/存貨金額
=(銷售總利潤/銷售成本)*(銷售成本/存貨)
=(銷售成本利潤率)*(庫存週轉率)
需要說明,這裡為什麼不使用銷售額/存貨來表示庫存週轉次數,因為如果有的企業銷售額會員高於銷售成本,此時並不能真實反饋現場改善而帶來的收益能力。
這裡得出的收益能力可分解為總部所應負責的銷售成本利潤率以及在生產、物流現場透過縮短過程時間以及實現準時化生產的庫存週轉率。
三、精實生產實踐之路探索
前面講到全域性最優並非區域性最優的結果導向,而目前在生產和銷售新商品時,很多情況下我們會引入成本企劃,即由豐田流出的成本管理手法。這種辦法首先時設定利潤,然後推算成本,即所謂的目標成本,然後依次拆解給各部門需要削減的成本金額,從而進行改善活動,但是正如區域性最優的一般客觀性結果來說,各部門的單元化改善行為,往往與成本企劃的預期目標背道而馳。
那麼具體應該怎麼去執行以及監測,這個時候我們應該跳出傳統的成本思考範疇,選擇前文所提到的收益性,其單位為元*天,即以縮短過程時間為重心進行思考改善。無論從採購、銷售、生產角度,對相應的時間也要進行更詳細的交涉,依次考慮對於收益性的影響。
結語
就多數離散製造企業來說,精實生產的理念其實已經融入於現場之中,只是在財務層面缺乏更細粒度的指標來衡量其改善結果,同時在改善層面也因繁瑣的審批流程及制度將改善點以惰性覆蓋。因此,一定要將“現在是最好的,現在就是好的”想法摒棄,徹底作好自動化,不斷追求準時化以獲得最大收益。
熱門文章推薦:
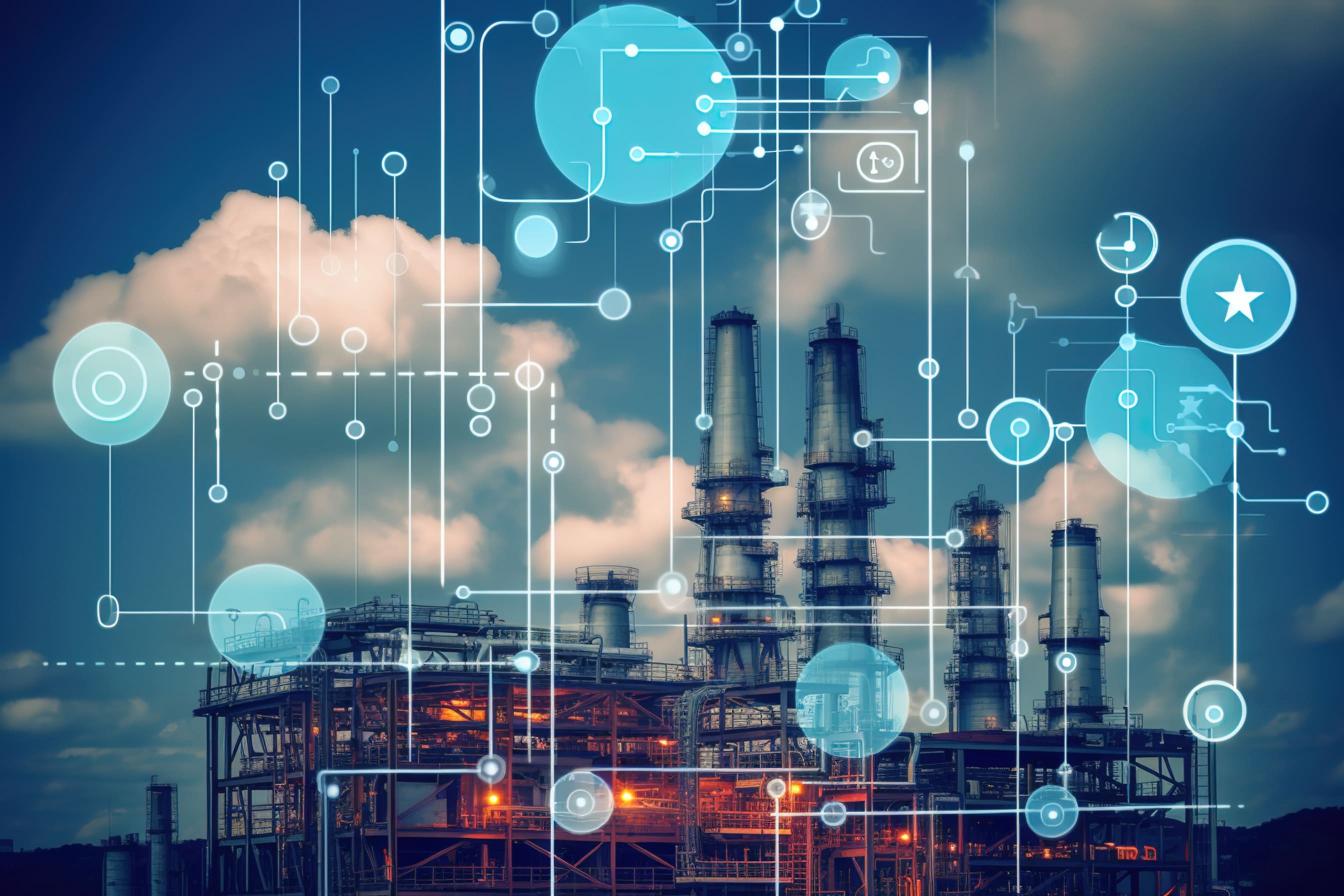
文 | 軟妹
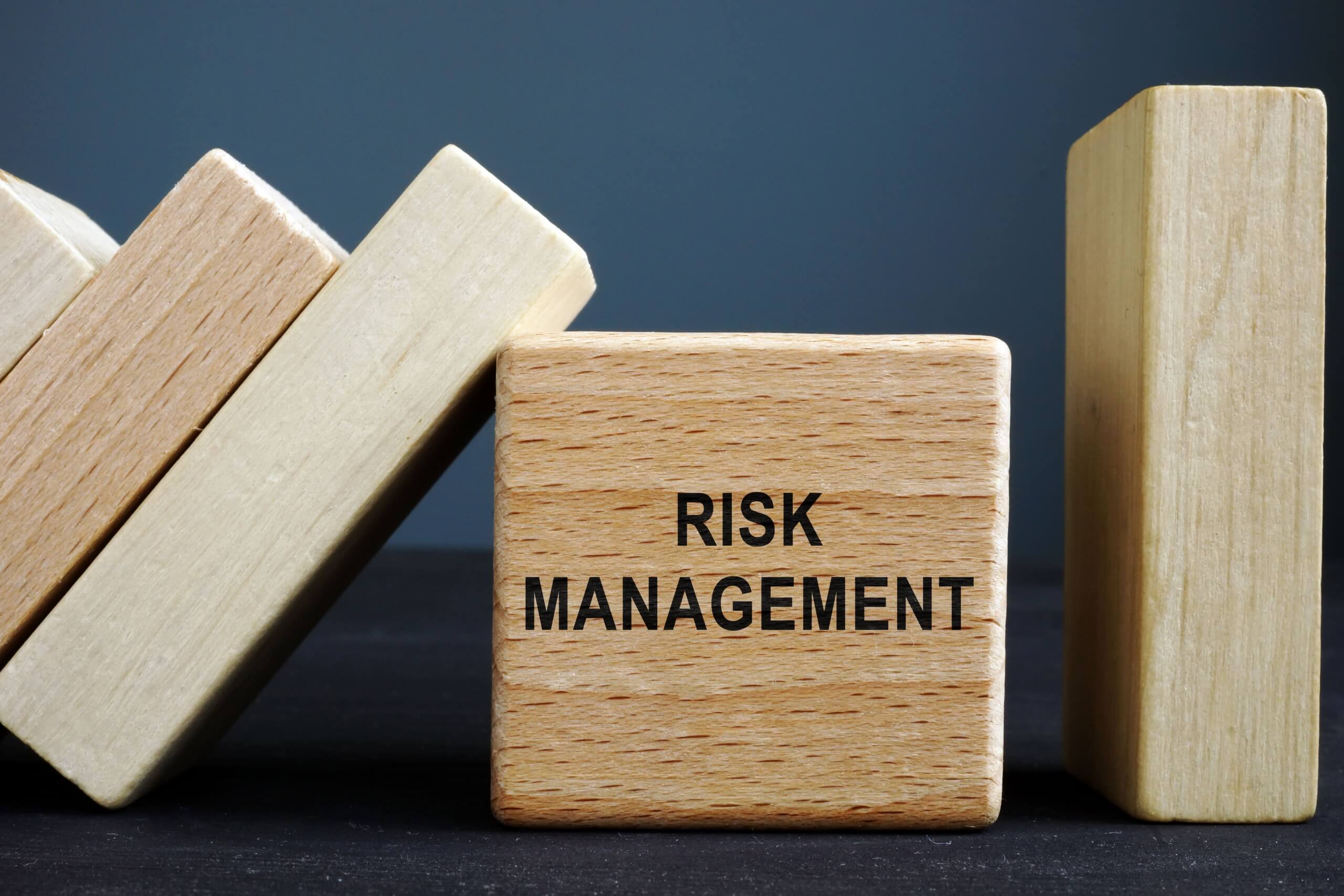
文 | 軟妹
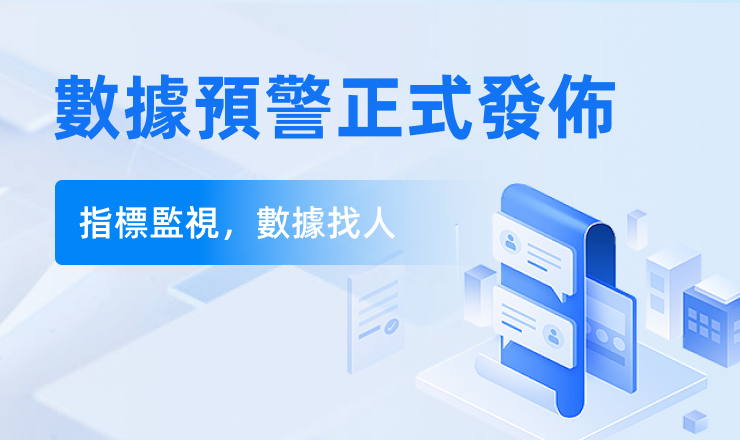
文 | 軟妹
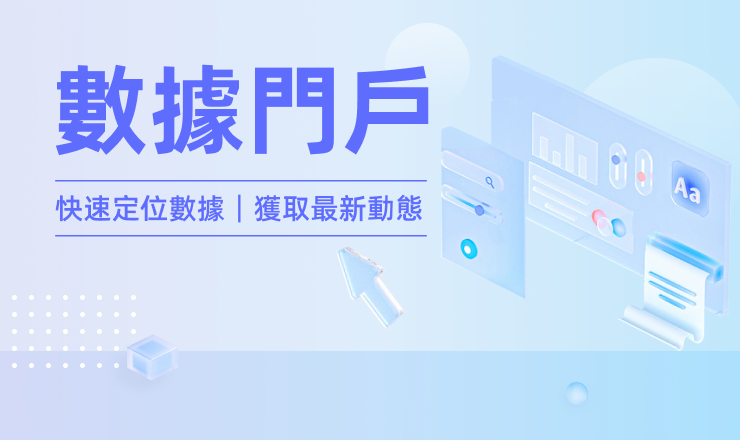
文 | 軟妹
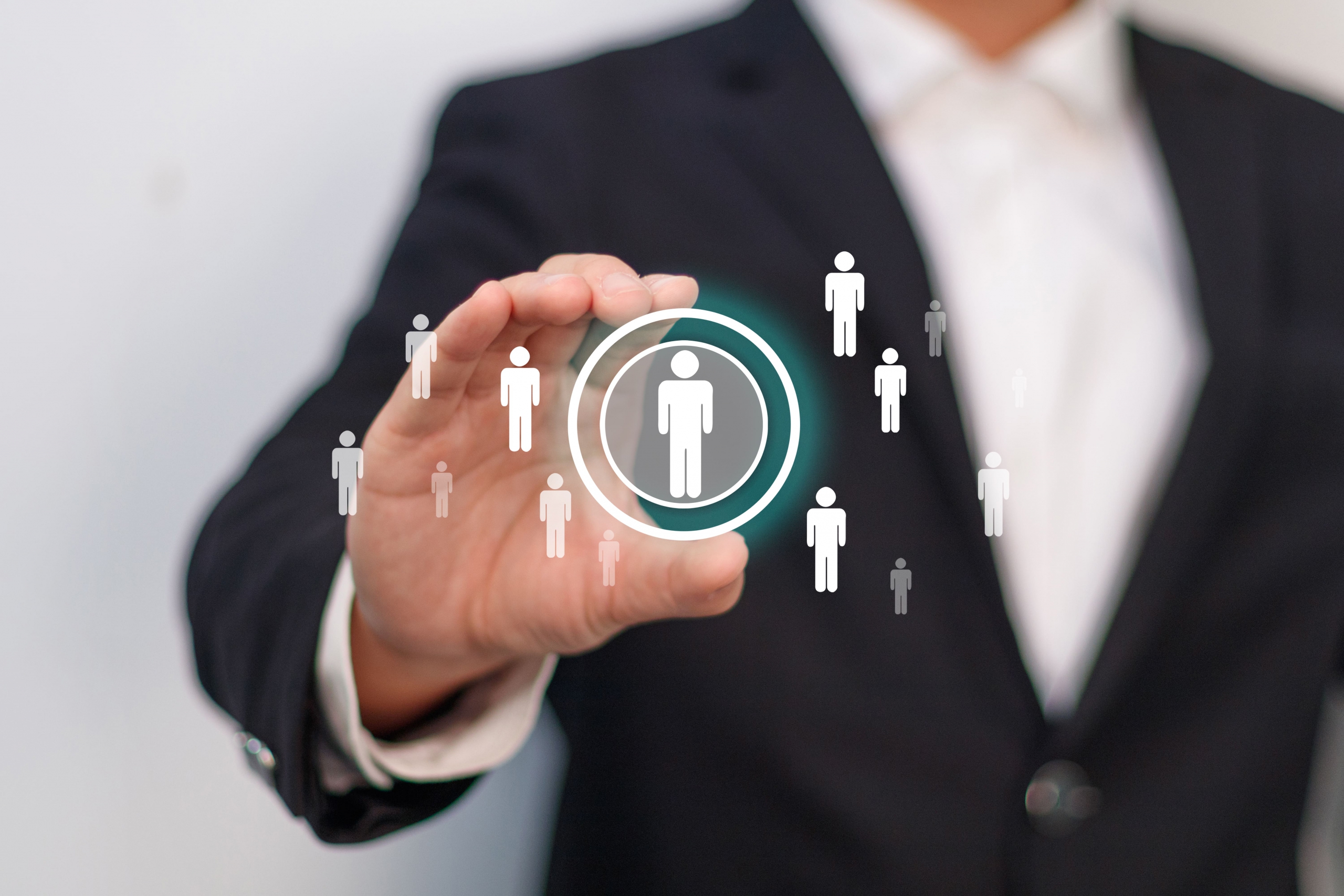
文 | 軟妹
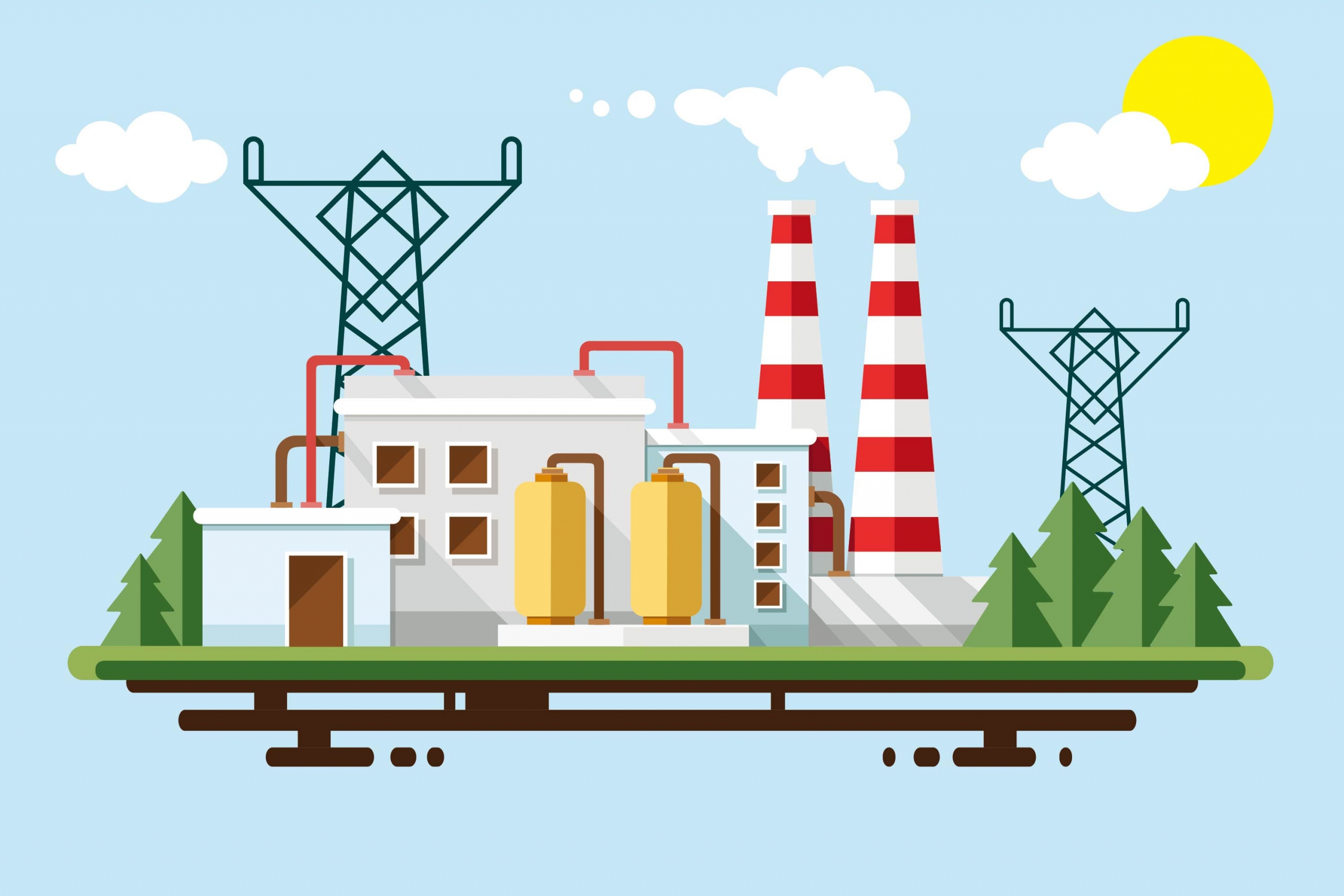
文 | 軟妹
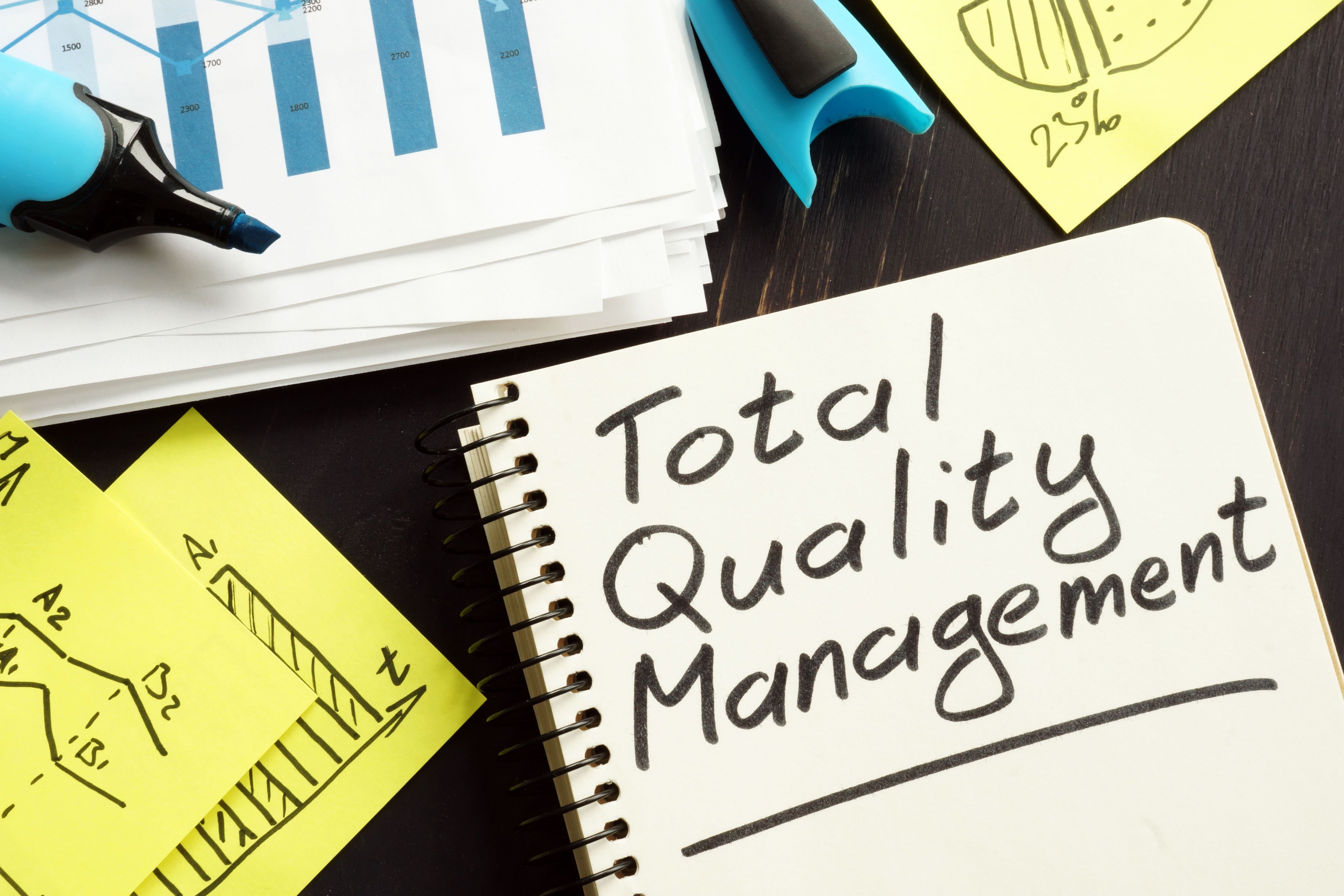
文 | 軟妹
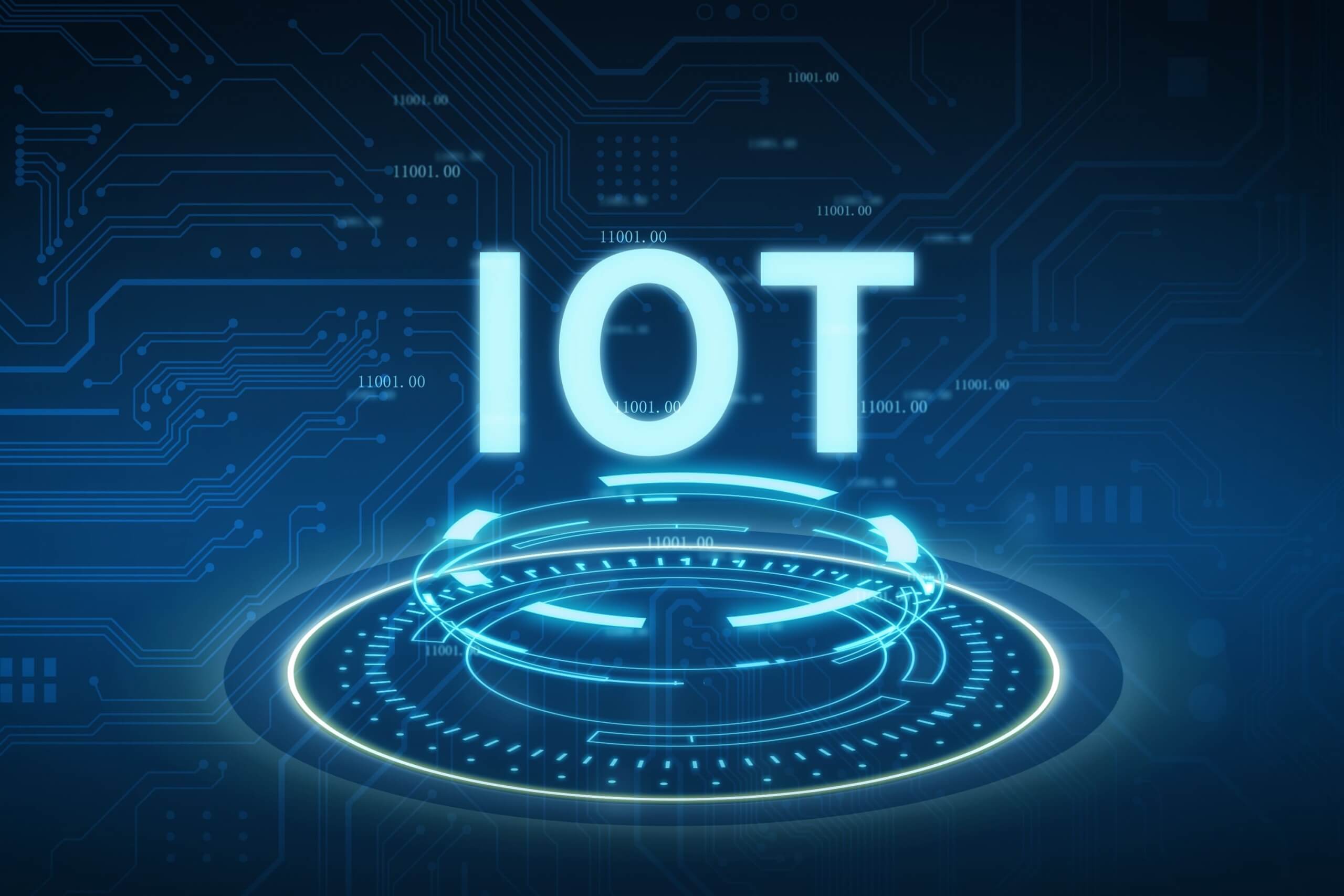
文 | 軟妹

文 | 軟妹
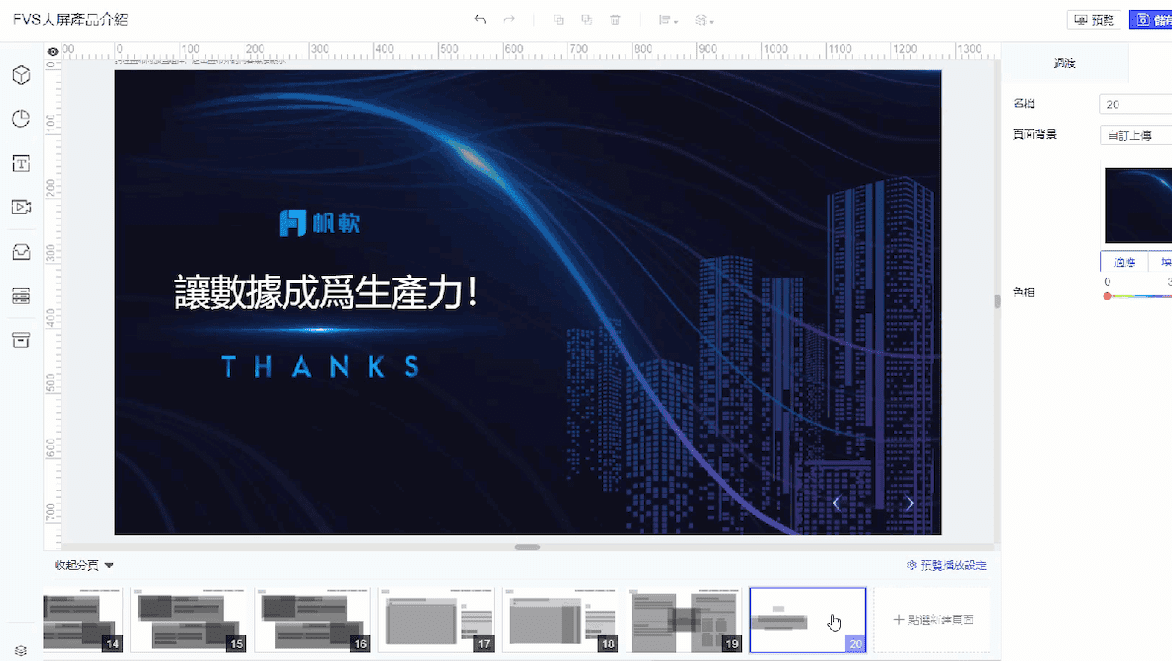
文 | 軟妹
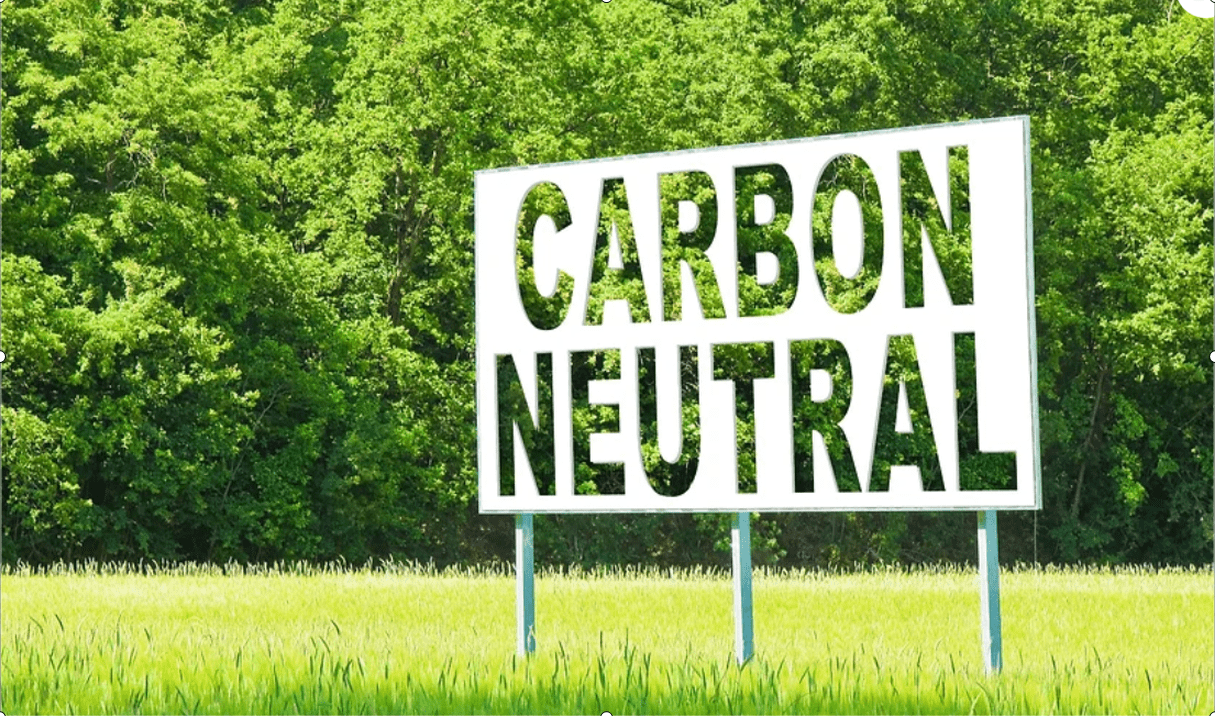
文 | 軟妹
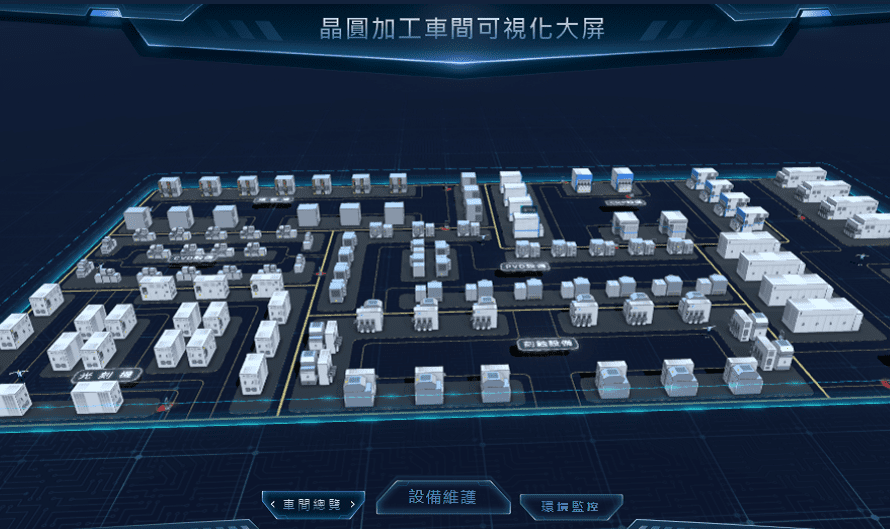
文 | 軟妹
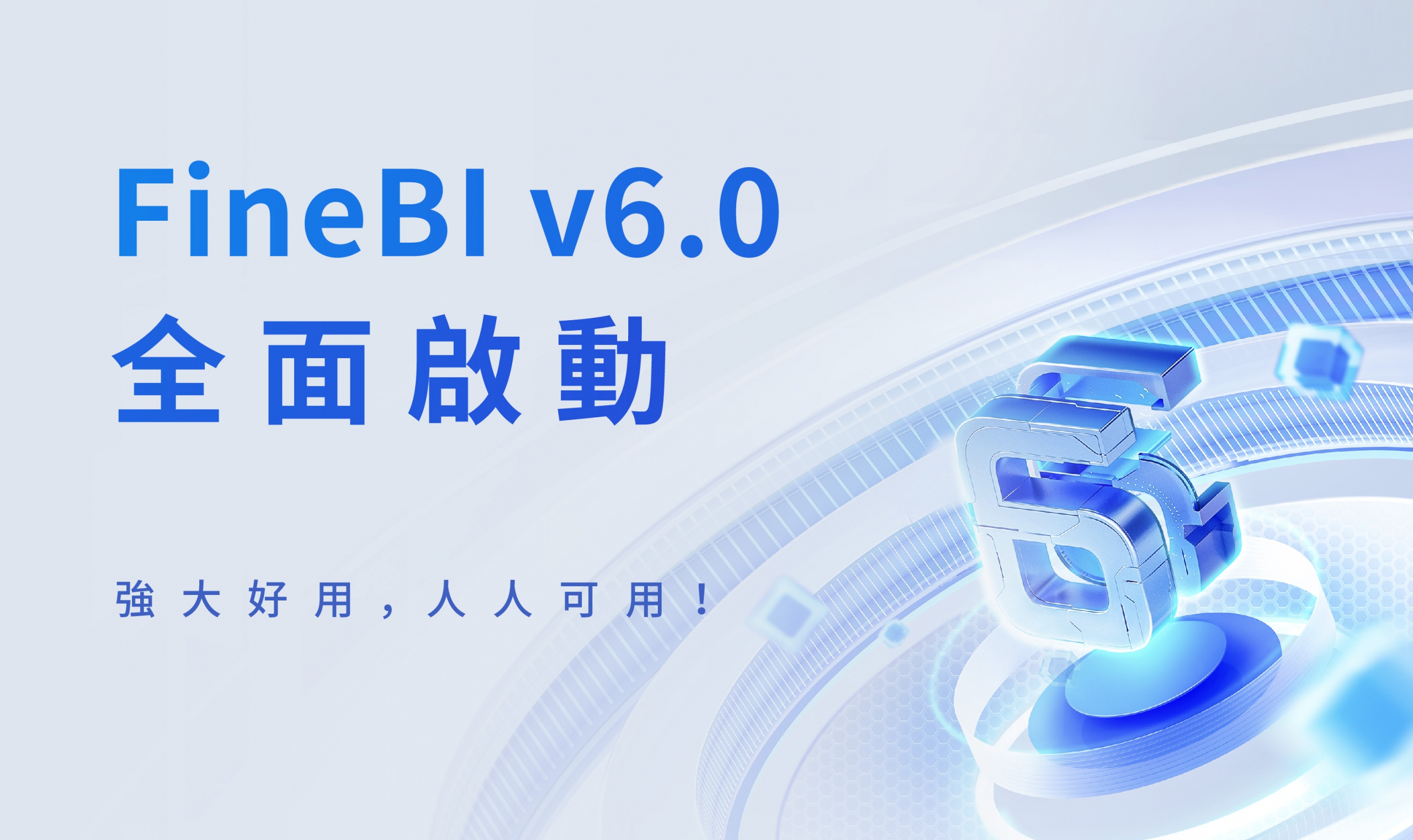
文 | 軟妹
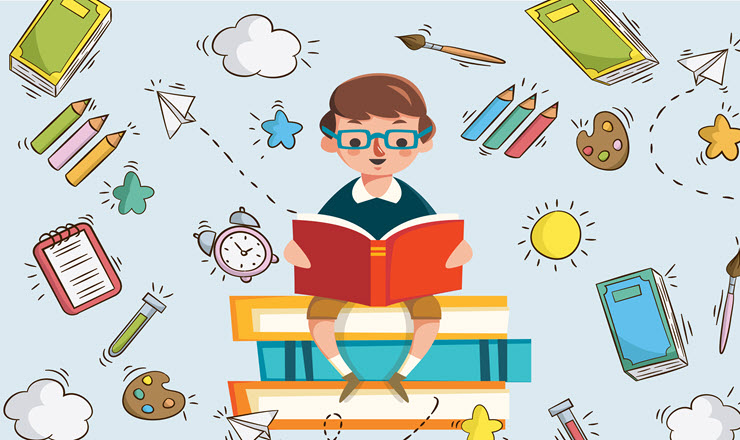
文 | 軟妹
.jpg)
文 | 軟妹
.jpg)
文 | 軟妹
.jpg)
文 | 軟妹
.jpg)
文 | 軟妹
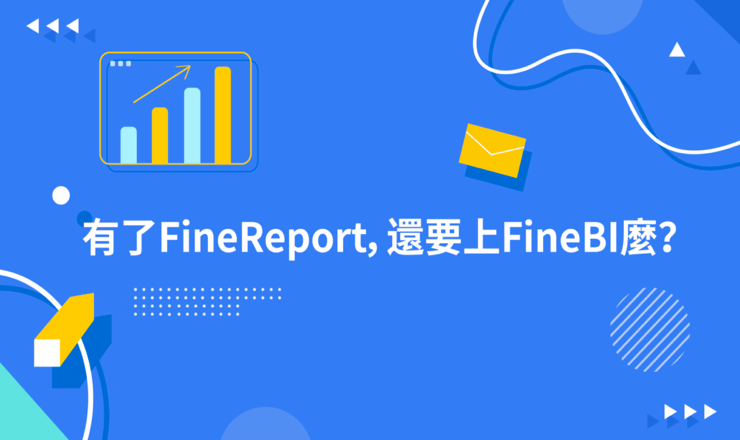
文 | 軟妹
.jpg)
文 | 軟妹
.jpg)
文 | 軟妹
.jpg)
文 | 軟妹
.jpg)
文 | 軟妹
.jpg)
文 | 軟妹
.jpg)
文 | 軟妹
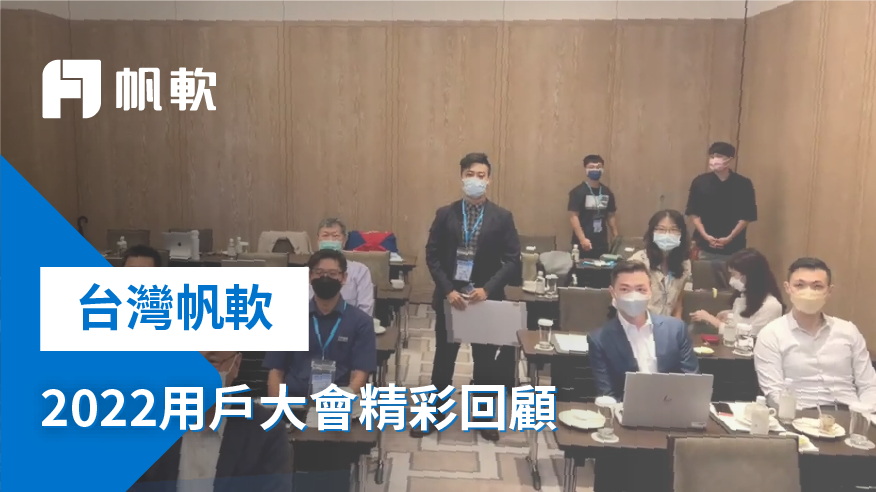
文 | 軟妹
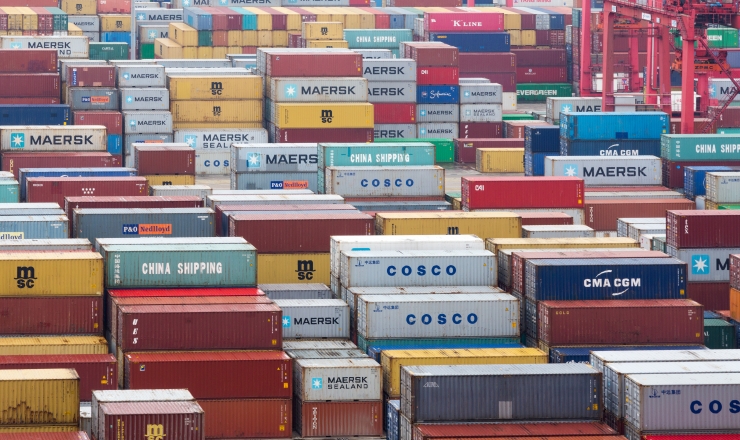
文 | 軟妹
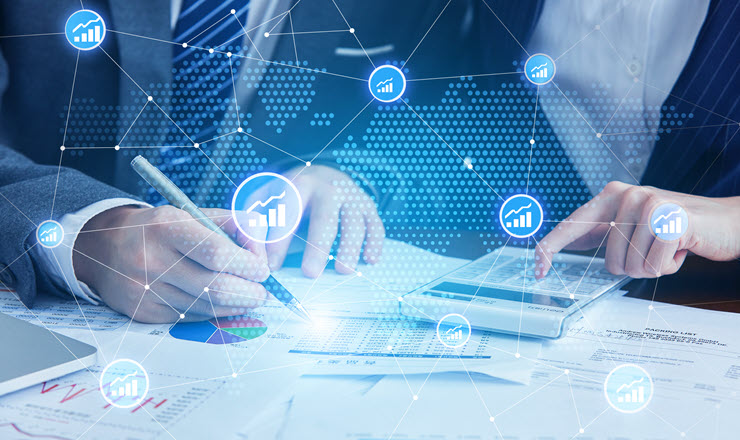
文 | 軟妹
_副本.jpg)
文 | 軟妹
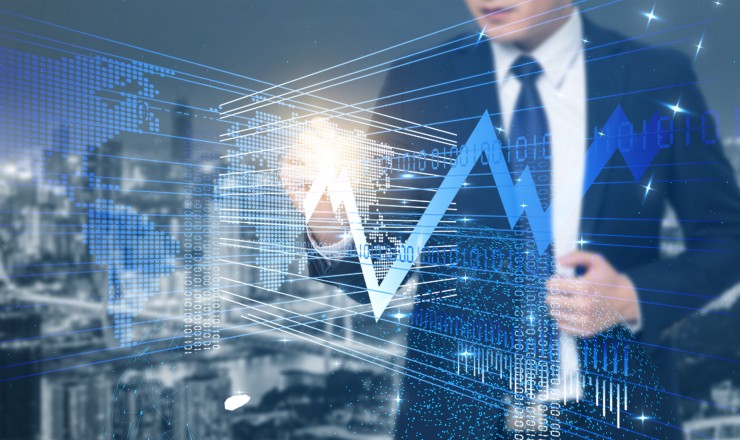
文 | 軟妹
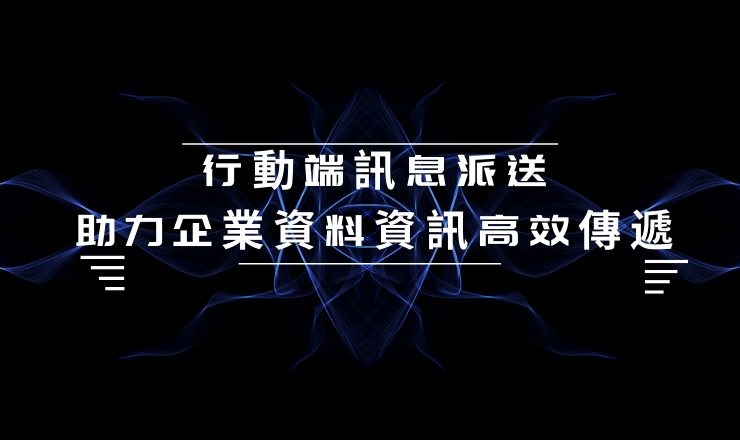
文 | 軟妹
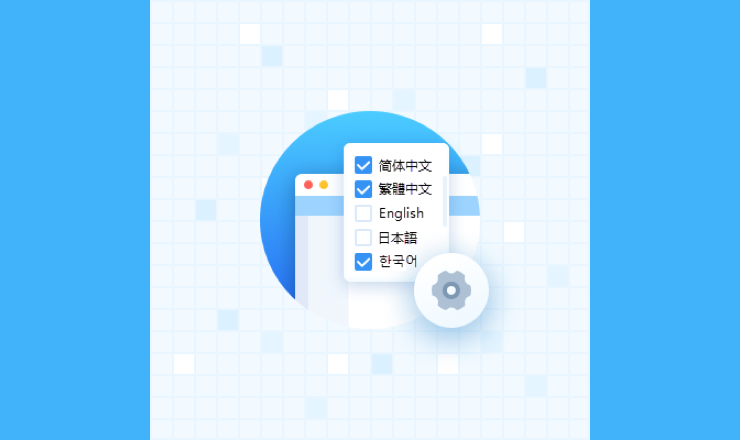
文 | 軟妹
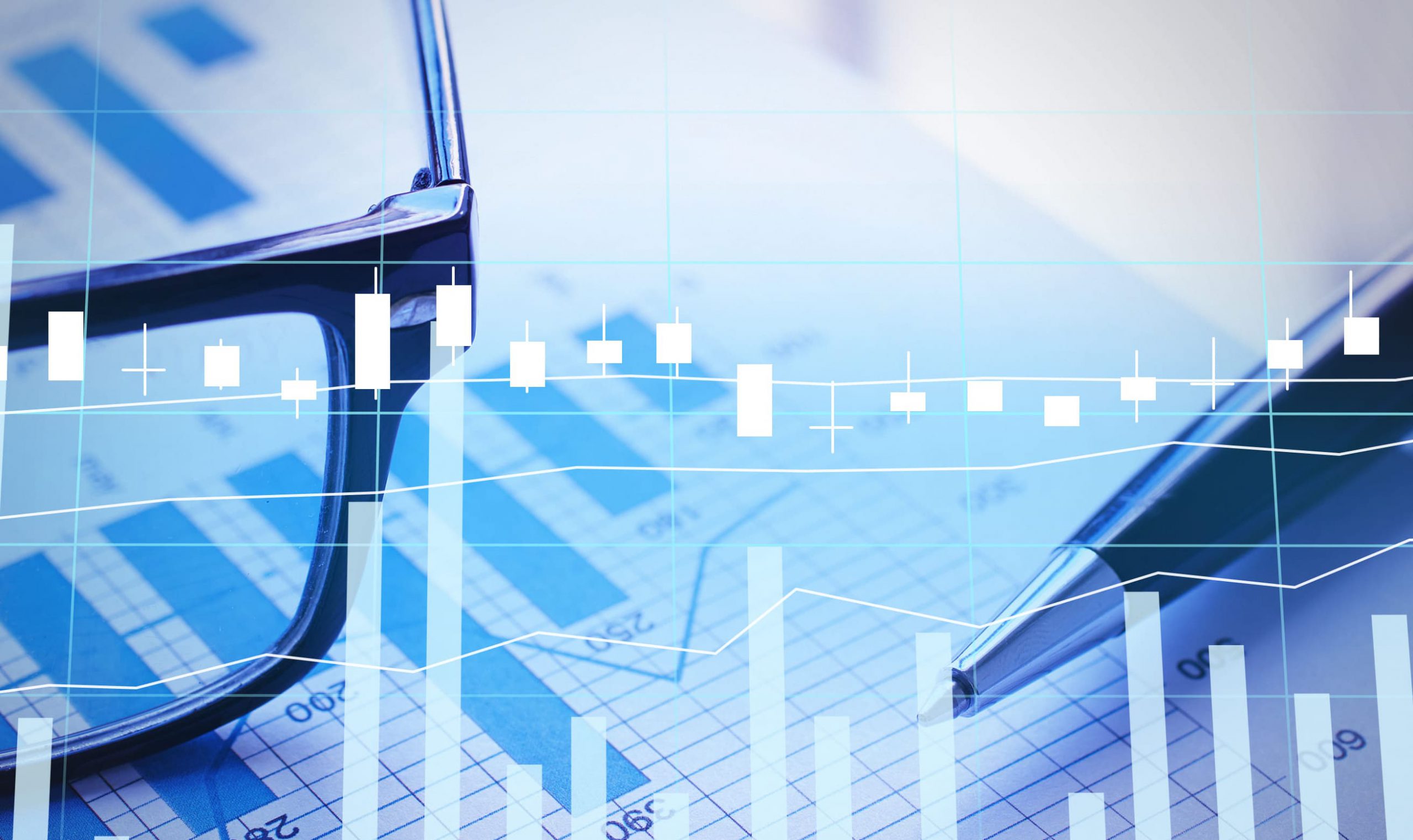
文 | 軟妹
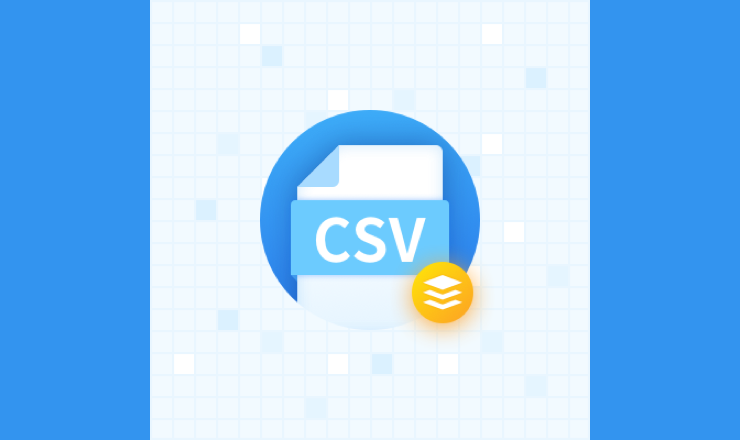
文 | 軟妹
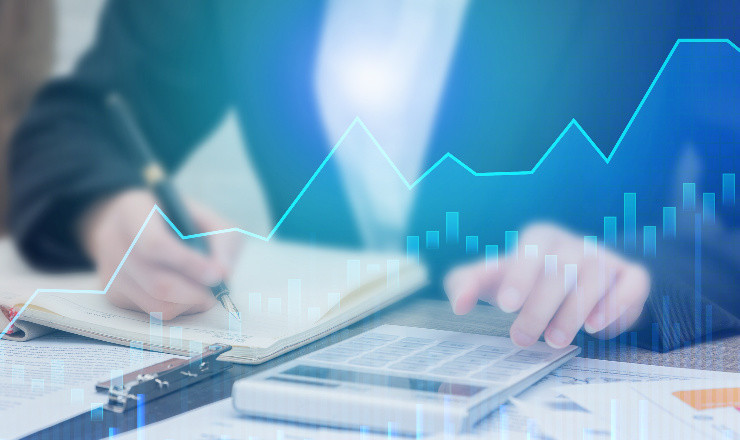
文 | 軟妹
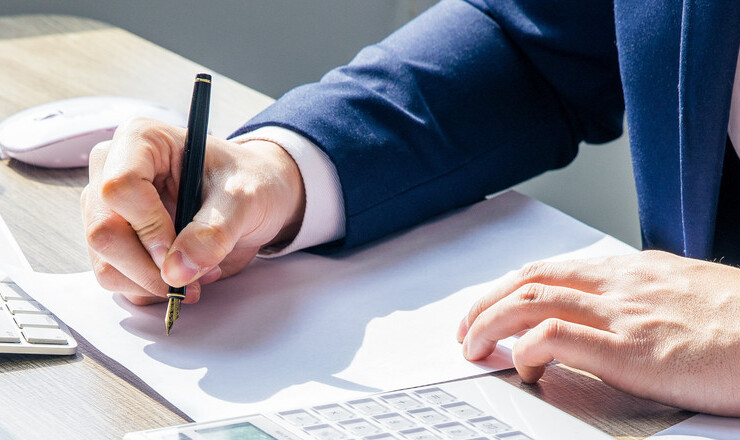
文 | 軟妹
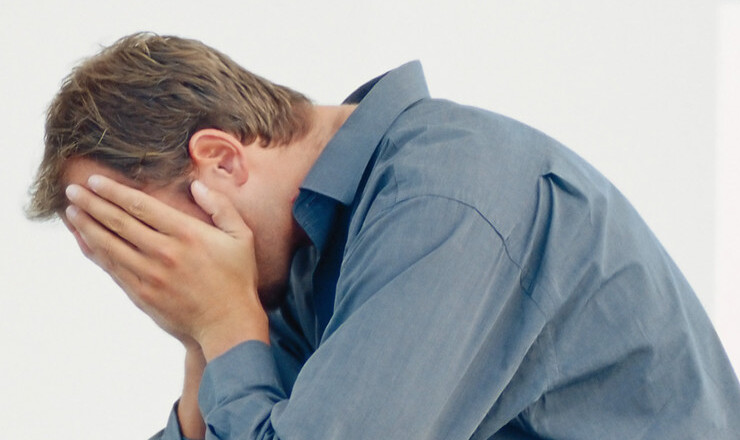
文 | 軟妹
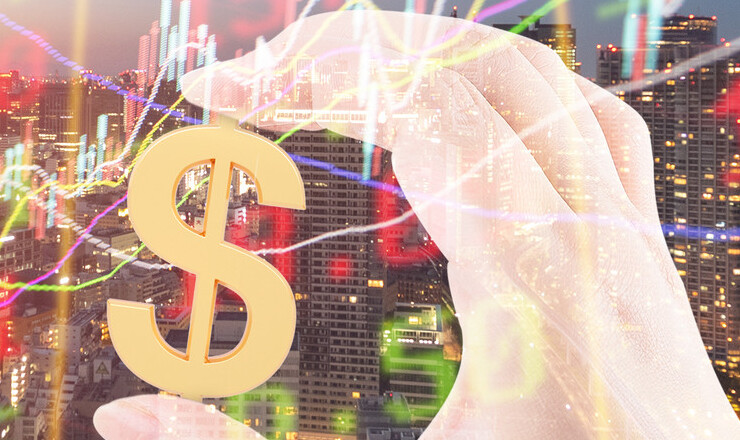
文 | 軟妹

文 | 軟妹
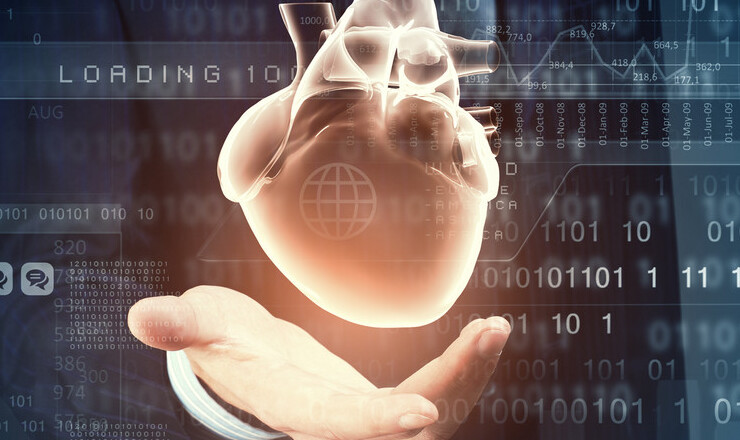
文 | 軟妹
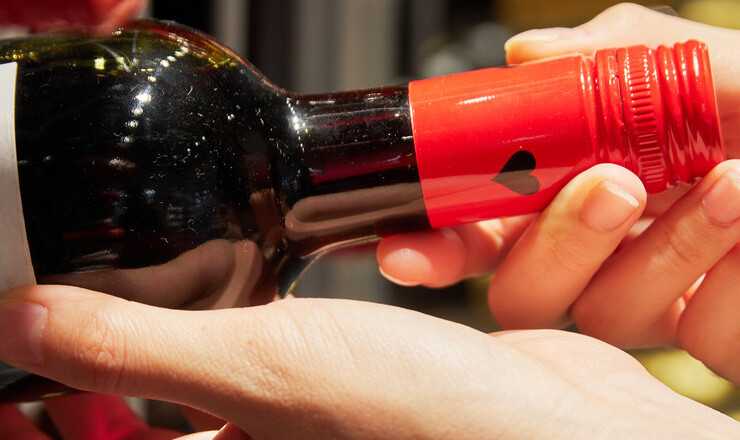
文 | 軟妹

文 | 軟妹
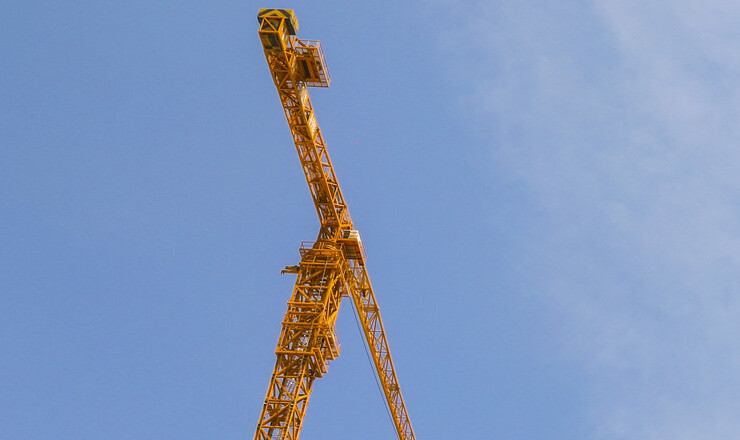
文 | 軟妹
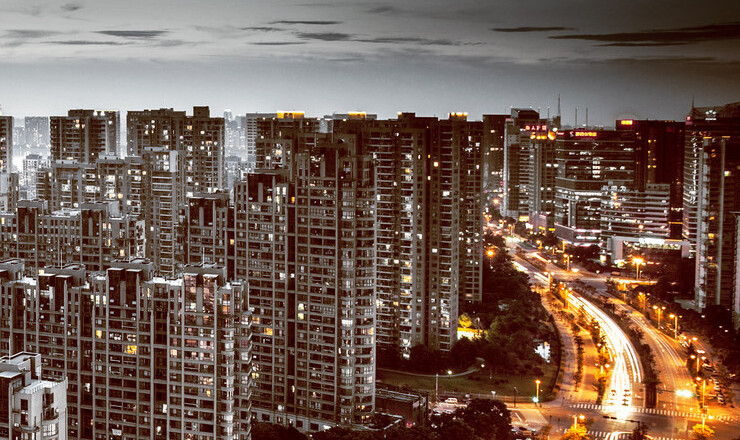
文 | 軟妹
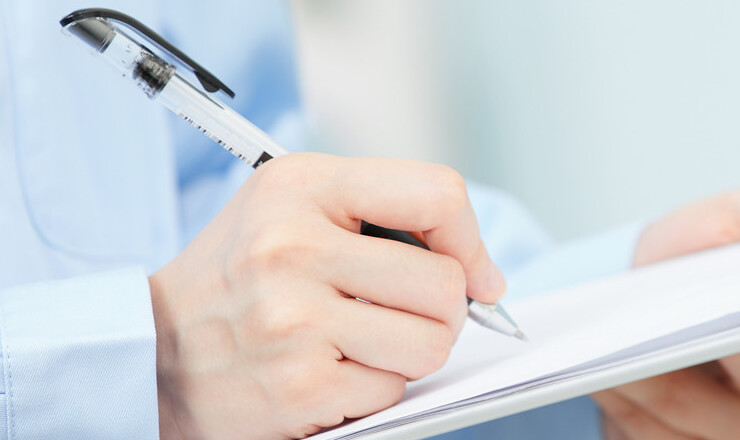
文 | 軟妹
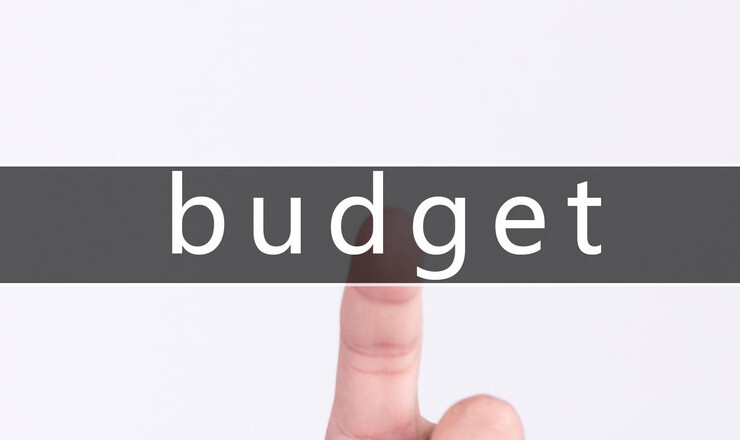
文 | 軟妹
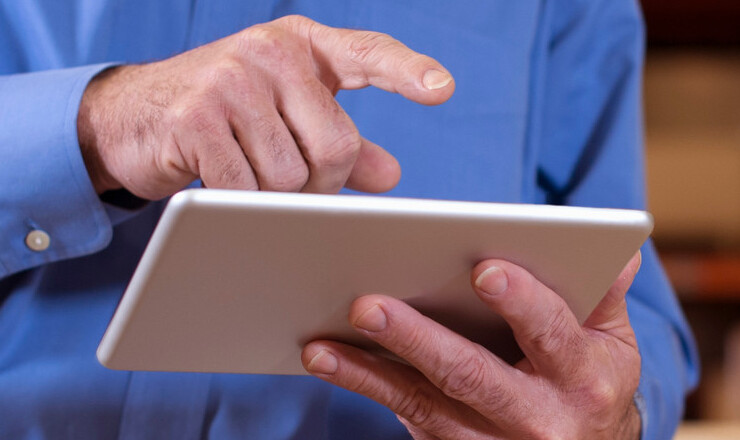
文 | 軟妹
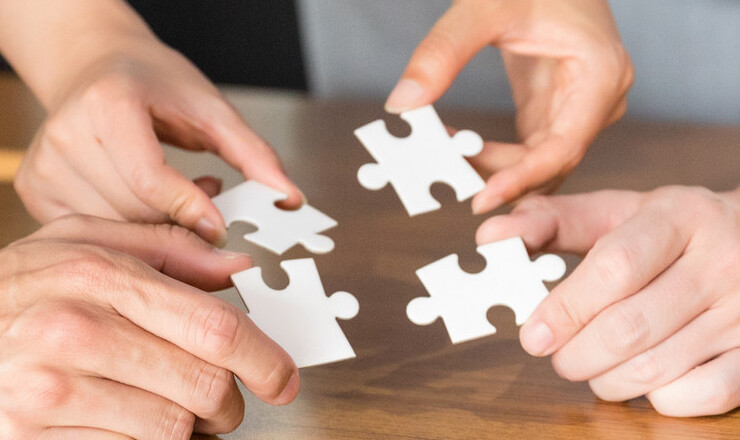
文 | 軟妹
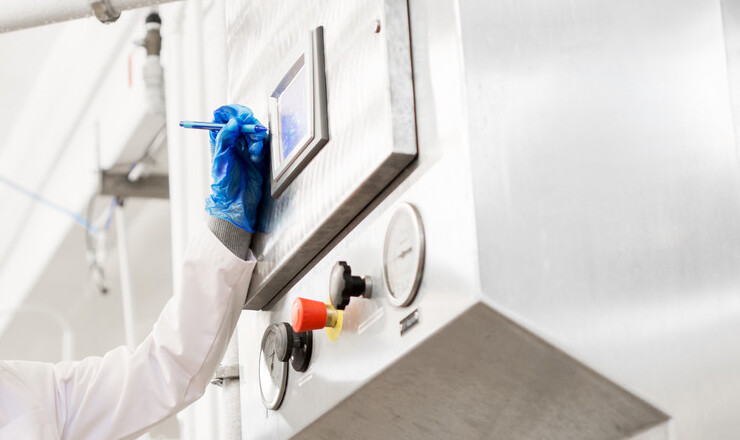
文 | 軟妹